JH Explorer in Sweden: Sunrise on green steel
Portfolio manager Tal Lomnitzer shares his excitement having seen how green steel is produced on a recent trip to the HYBRIT project in Sweden.
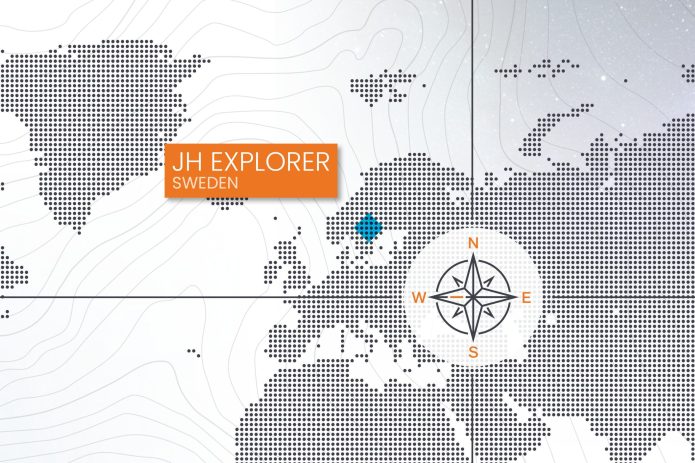
3 minute read
Key takeaways:
- The global steel industry produces around 7% of global CO2 emissions due to the blast furnace coking coal approach.
- Green steel can be made using hydrogen instead of coking coal as a reducing agent, producing H2O as the by-product instead of CO2.
The JH Explorer series follows our investment teams across the globe and shares their on-the-ground research at a country and company level. |
Luleå in far Northern Sweden is worth visiting as a tourist for the ‘midnight sun’ in the peak of summer when the sun does not set – instead one gets hours of sunset when it would normally be dark. My visit was purely work related to see a different kind of sunset – that of the way steel is currently produced. The objective of my visit was to see the production of truly green, carbon-free steel at the HYBRIT pilot project, a joint venture between Swedish steel manufacturer SSAB, renewable power producer Vattenfall and high-quality iron ore producer LKAB. The HYBRIT technology used could potentially reduce Sweden’s total CO2 emissions by at least 10%, but more importantly could lead to a reduction in emissions from iron and steel production globally.*
At SSAB’s LuleÃ¥ steel manufacturing plant they take high-grade iron ore pellets, heat it with coking coal to remove the oxygen, leaving pure molten iron and carbon dioxide. The blast furnace coking coal approach means that the global steel industry produces around 7% of global CO2 emissions**. This is why I was so excited to visit a project that uses hydrogen instead of coking coal, as a reducing agent. Â
The same molten iron is produced but instead of CO2, H2O is the by-product. This is truly ‘green steel’, assuming that the hydrogen used is green hydrogen made with renewable electricity. I was amazed to find out that in Northern Sweden there is capacity for about 20 terawatt hours of excess renewable electricity to make hydrogen to feed this process. That power could make a lot of green hydrogen. Good thing too because humanity is going to need a lot of steel to build wind farms, solar farms, and grid infrastructure to power a decarbonised, electrified future. We have the means, and I have now seen how steel can be made in a way that has a minimal environmental footprint.
This is so exciting – I feel like I have peered into the future to see the sun rise on a new dawn for the steel industry.
Goodbye blast furnaces – here is the old blast furnace that will be replaced with an electric arc furnace to melt briquettes using renewable power.
A fossil-fuel free briquette of pure iron in the palm of my hand.
Photos courtesy of Tal Lomnitzer, used with permission.
*https://www.hybritdevelopment.se/en
**UN Emissions Gap Report 2020.